The technique of molding or shaping plastic pieces around non-plastic parts, or inserts, is known as insert injection molding. The inserted component is usually basic, like a thread or rod, although inserts can be as sophisticated as a battery or motor in other circumstances. Read More…
For 50 years, LTM Plastics has been a leading manufacturer of injection molded plastics. When working with LTM Plastics, our customers can be assured that they are getting high quality products at a competitive price. We pride ourselves on our team’s communication and collaboration with our customers to meet their needs.
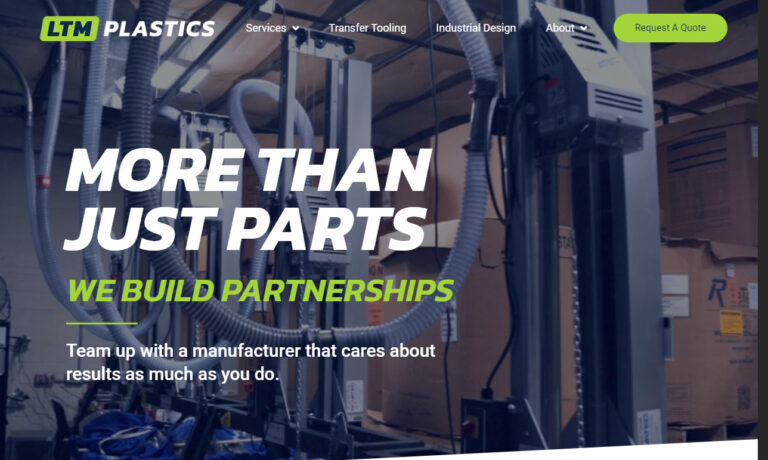
As one of the Midwest’s oldest plastic molders, Koller-Craft has craftsmanship built into its name. We take pride in our quality injection molding work. Large to small parts, short to long runs. Excelling at product design, prototyping, close tolerance molding, insert molding & secondary services.
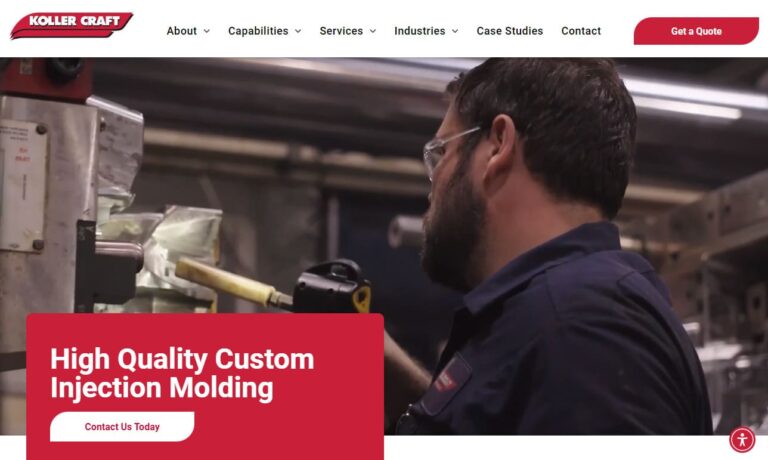
Hi-Rel Plastics & Molding, Inc. offers injection molding for a variety of industries. We can process an almost infinite variety of thermoplastic resins, our prices are competitive, our delivery is on time, and we provide superior customer service. Value-added services include label application, assembly services, and custom packaging and shipping. Our team has the knowledge and expertise to...
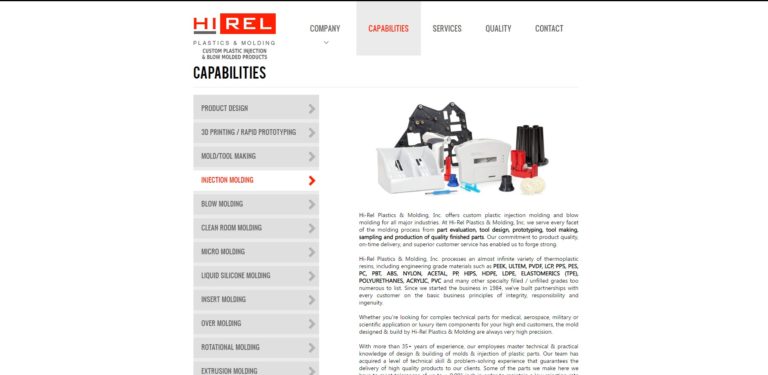
We may have started small, but today, we offer our products and services to companies around the world. We are dedicated to our customers, and our goal is to offer better service and pricing to any customer no matter the size.
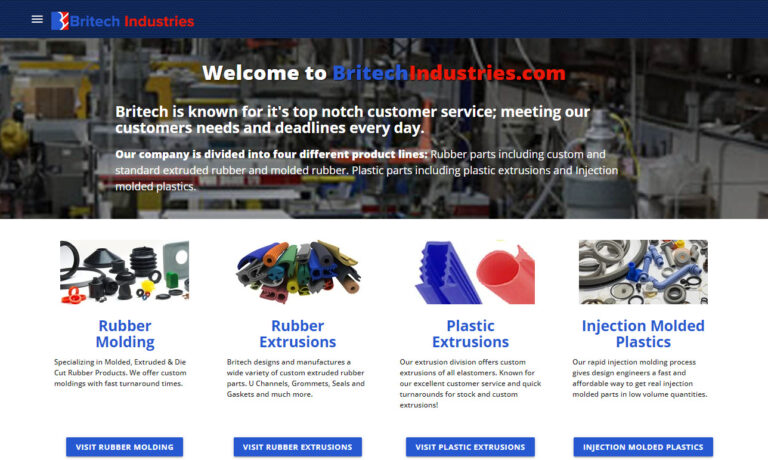
Our injection molding plastics services are designed to meet a wide range of applications. We work with various thermoplastics and provide custom molding solutions that ensure exceptional accuracy, strength, and durability. From small intricate parts to larger molded components, we tailor our approach to each project’s needs.

Valencia Plastics is your leading full-service injection molded plastics manufacturer. Our products are made with various materials, including urethane, polyurethane, nylon, acrylic, and polycarbonate. We offer a wide range of sizes from miniature items up to 7 lbs. large parts. We are ISO 9001:2015 compliant. Industries we serve include electrical, military, automotive, aerospace, and...
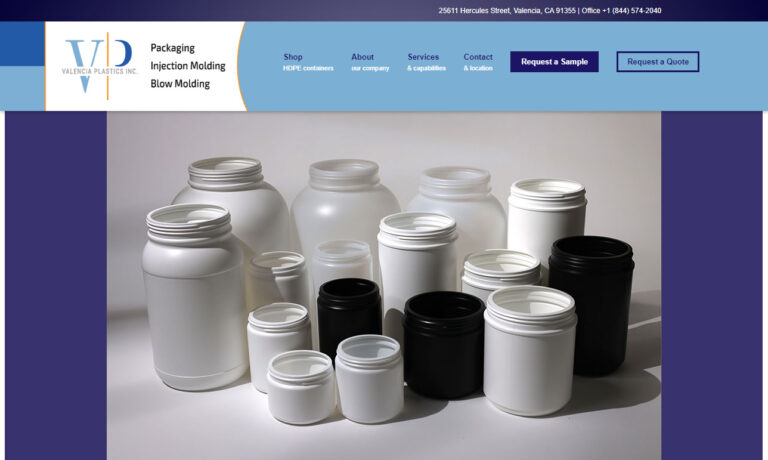
Abtec, Inc. is a manufacturer of injection molded thermoplastics for high-tech OEMs. Since 1981, we have provided quality injection molded plastics and engineering services to such industries as automotive, aerospace, dental, electronics, food handling, nuclear, reprographics and more. Our 21,000 square feet building operates 24-hours a day, 5 days a week. Contact us today!
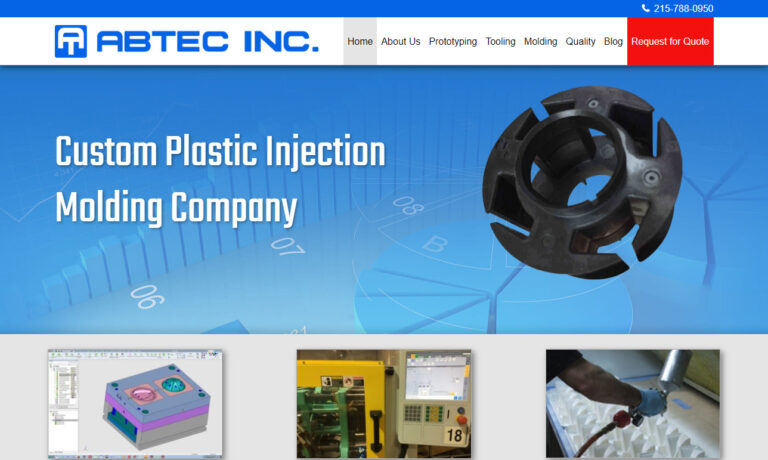
You won’t find better quality injection molded plastics anywhere else in the industry. We have built ourselves up from a small manufacturing company to a large company with decades of experience.
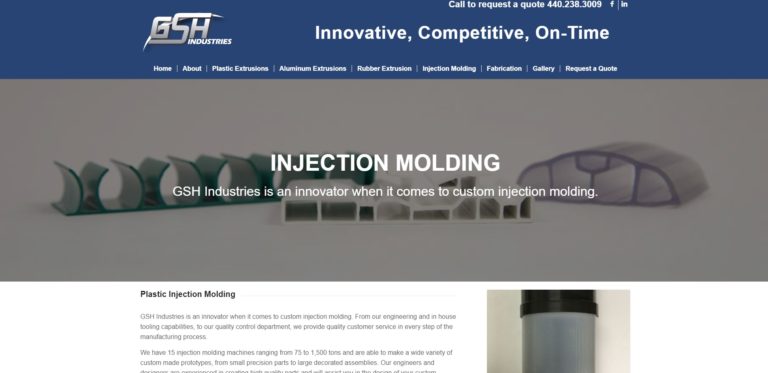
At EXI-plast Custom Moulding Ltd., we specialize in delivering high-quality injection molding solutions tailored to our client's diverse needs. With years of experience and advanced manufacturing capabilities, we excel in producing precision-molded components for various industries. Partner with us for reliable and customized injection molding solutions.
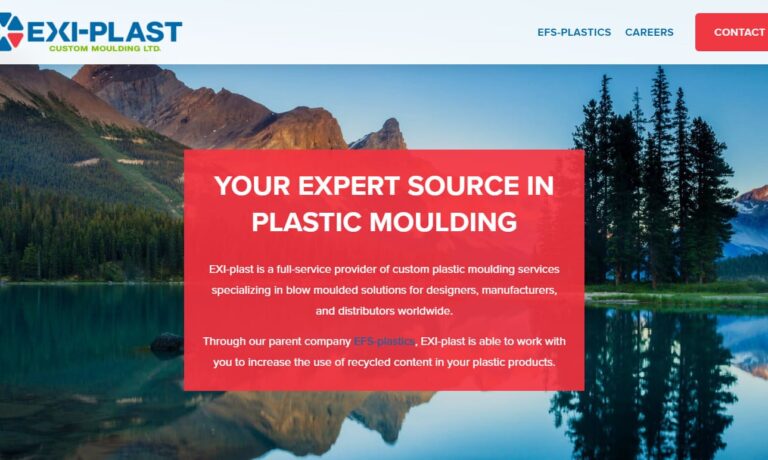
More Insert Molding Companies
What is Insert Molding?
Insert molding also integrates metal, plastics, and other materials and components into a single unit. For example, engineering polymers are used for enhanced wear resistance, tensile strength, and weight reduction, while metallic materials are used for strength and conductivity.
Insert molding is commonly used to include one or more threaded metal inserts in a plastic part that is meant to join with another part in an assembly. However, plastics may not have the mechanical qualities necessary to sustain the forces required to join two pieces.
For example, thread in a plastic part might wear out with repeated use, resulting in a failed item. Metal inserts enhance the plastic's characteristics and ensure the portion stays fastened over time.
Using this mix of plastic and metal, designers can use plastic's weight reduction and metal's robustness.
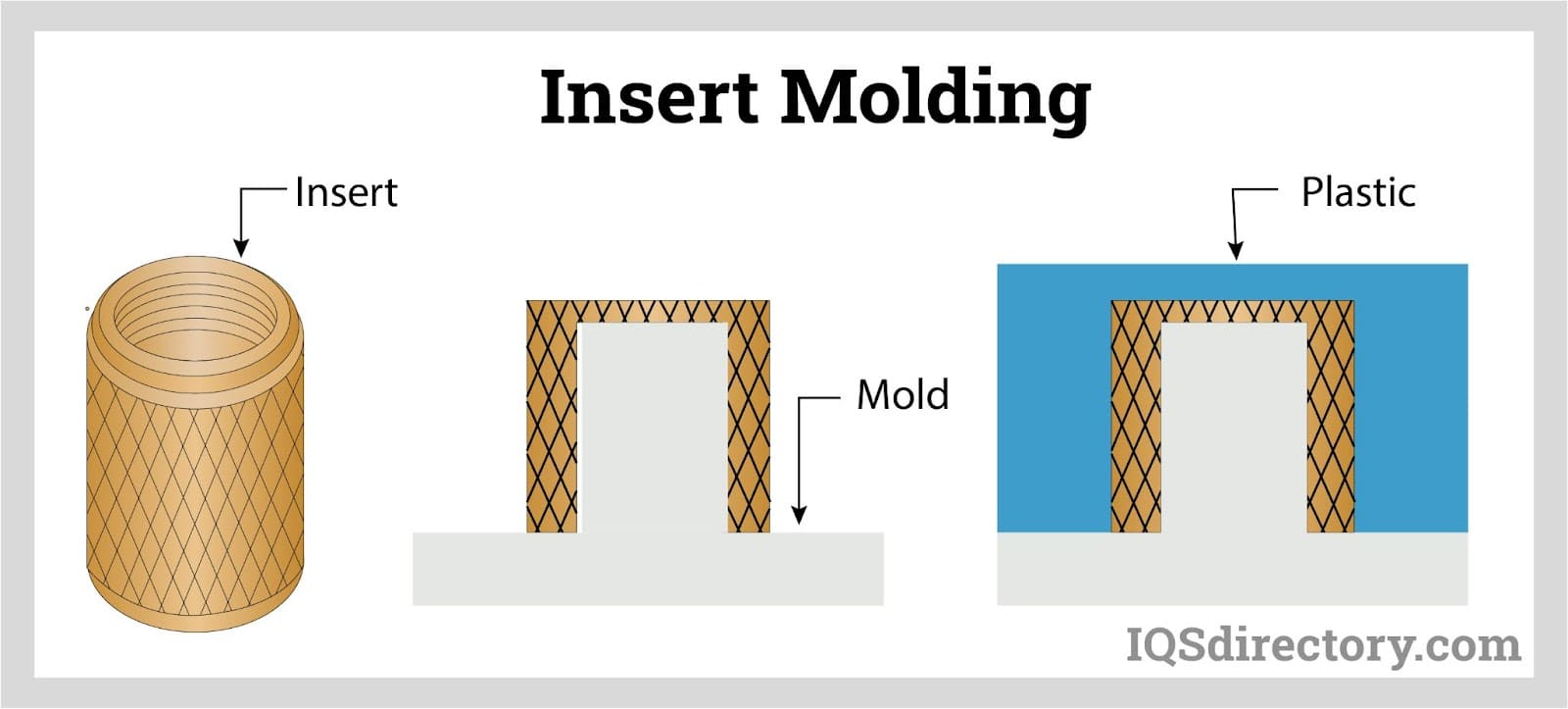
Insert Molding Process
The injection molding process remains the same regardless of which equipment is utilized. The machine's barrel part is heated in the first stage. Placing the pellets, or grains, into a hopper is the next step.
A screw mechanism inside the hopper drives the granules into the heated barrel, where they are melted down. Next, a split die chamber mold cavity is injected with molten plastic. The cavity is clamped shut once it is full.
Water and other fluids circulate through the mold's cooling system, removing the heat. The portion is held in the mold under extreme pressure until it hardens entirely. Finally, the part is taken from the mold once it has solidified.

The most frequent material utilized in the injection molding process is thermoplastics. On the other hand, elastomers, biodegradable polymers, and thermosets can be employed. ABS, polycarbonate, and polypropylene are additional materials that can be utilized for injection molding.
The insert molding process needs exceedingly tight tolerances to properly create the plastic parts being made. The tiniest misalignment can cause the molding process to fail. As a result, manufacturers may use a different type of plastic during the fabrication process to keep prices down.
Costs can be kept low by researching the benefits and drawbacks of various varieties of plastic. Not all plastics, for example, can be recycled; nevertheless, polystyrene, polyethylene, and nylon can.
Recycling and reusing plastics is one of the most cost-effective ways to save money during manufacturing.
Advantages of Insert Molding
- Increases Design Flexibility: Insert molding enables nearly limitless permutations, which benefits designers. Overmolding, for example, allows a 3D circuit board to travel freely inside and outside, into holes, and up walls of the part, with the plastic connecting it.
- By combining various components with thermoplastic, insert molding helps reduce assembly and labor expenses. For example, a single stamping can be perforated after overmolding to produce many circuit routes.
- Increases Reliability: Because each part is firmly held in thermoplastic, an insert molded component avoids loosening, faulty terminations, misalignment, and other issues, resulting in increased component reliability. Vibration and shock resistance are also improved using thermoplastic resin.
- Insert molding produces components that are smaller in size and lighter in weight because it eliminates the need for connectors and fasteners and combines the physical strength of metal inserts with resin.
- The technique offers a high production rate and requires little to no additional processing after the injection molded object is completed.
- Injection molding is the method of choice for producing exceedingly intricate products that can't be made any other way.
Applications of Insert Molding
- Military hardware
- In-mold labeling (IML) and in-mold decorating (IMD)
- Tube valves and needle hubs
- Encased bushings, studs, and tubes
- Appliance knobs, assembly knobs, and control knobs
- Threaded fasteners
- Electrical components and electronic gadgets
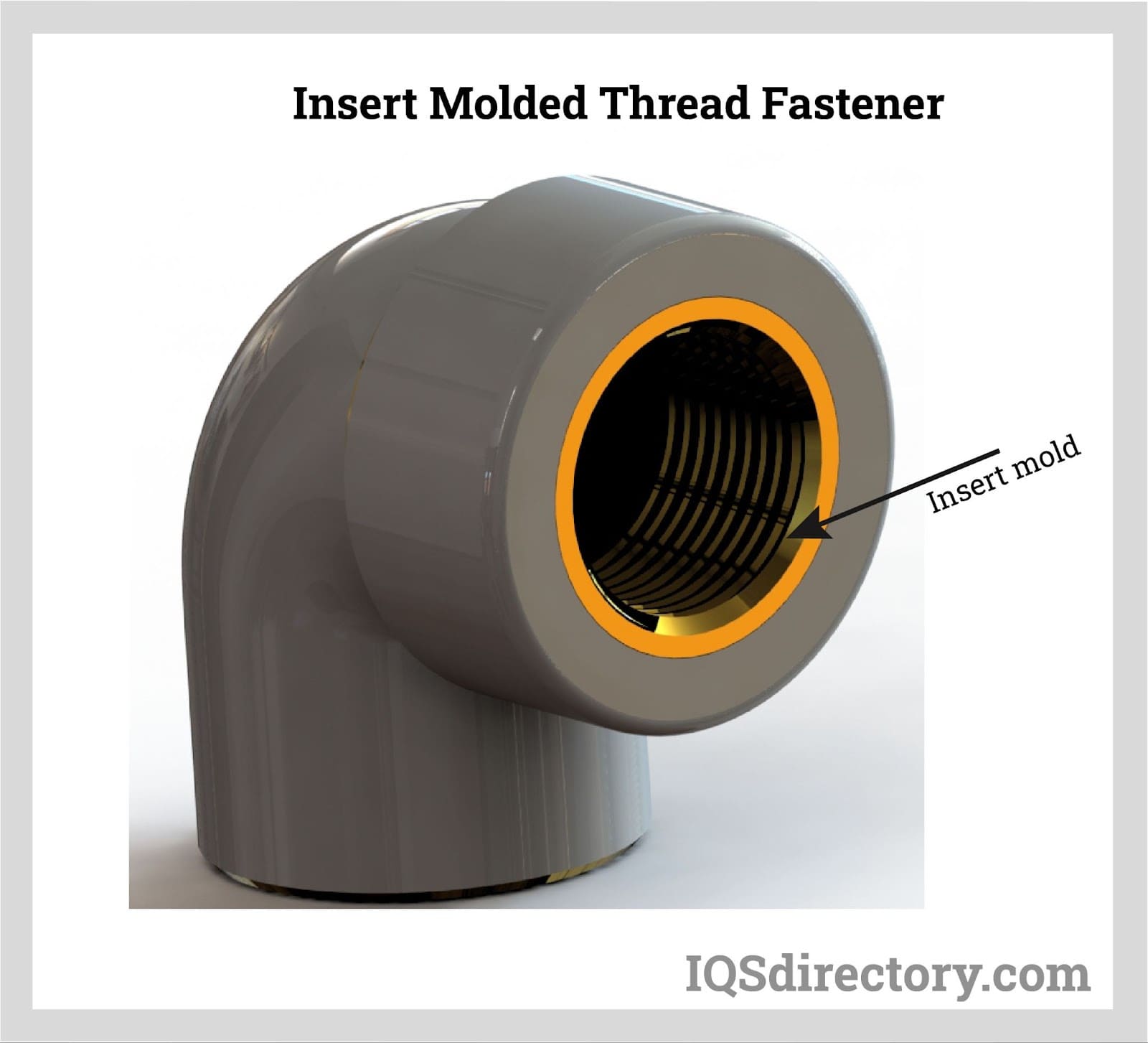
Choosing the Proper Insert Molding Company
To make sure you have the most productive outcome when purchasing Insert Molding from an Insert Molding Company, it is important to compare at least 6 Manufacturers using our Insert Molding directory. Each Insert Molding Company has a business profile page that highlights their areas of experience and capabilities and a contact form to directly communicate with the manufacturer for more information or request a quote. Review each Insert Molding business website using our proprietary website previewer to get an idea of what each company specializes in, and then use our simple RFQ form to contact multiple Insert Molding businesses with the same quote.